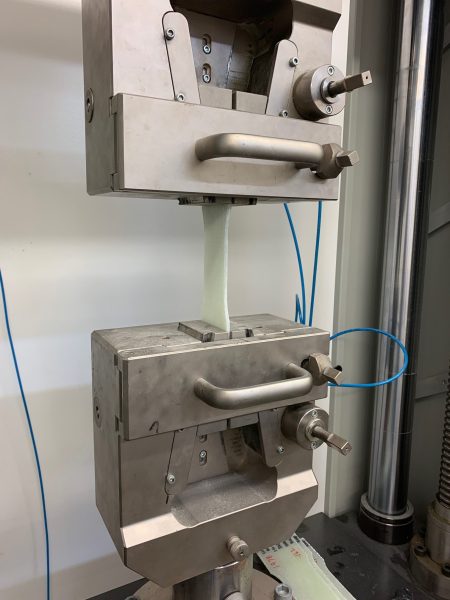
Cured-in-Place (CIPP) has transformed the rehabilitation of underground pipelines through its innovative approach and cost-efficiencies. A high level of quality control is imperative to achieve a high standard of materials, structural performance and longevity of the rehabilitated pipelines in reference to industry standards such as ASTM F1216, ASTM F1743 and guidelines by NASSCO and the American Water Work Association.
As the manufacturer of E Squared Flexpipe™ coated felts for CIPP lateral and mainline applications, we would like to provide further insights on critical quality control criteria in the manufacturing of high-quality thermoplastic coated liners that are compatible with thermosetting resin systems.
High performance USA manufactured polyurethane (TPU) and polyolefin (TPO) resins are carefully selected to provide the required mechanical performance, chemical and abrasion resistance, hardness levels and thermal performance in the manufacturing of coated liners on a variety of fiber materials including non-woven and fiberglass in widths up to 116″. Coating thickness ranges between 5 and 25 mils on fiber materials, subject to liner application.
Prior to production, the incoming resins are tested in the laboratory to evaluate properties such as melt flow/viscosity consistency, film quality and clarity to ensure a stable extrusion coating process.
During production, polymer coating thickness and weight density are monitored real-time using online gage measurement devices to ensureuniformity across the web and length of the liner. Manufacturing process with proper drying equipmentto eliminate excessive moisture content in TPU, precise extrusion die and extrusion processcontrols (temperature, pressure, torque and speed) is necessary to maintain a homogenous extrudate and effective saturation of molten polymer on fiber substrates for maximum coating adhesion. Maximum coating adhesion to the fiber substrate without pin holes is critical to prevent delamination and failure of TPU/TPO coating during the wet-out, inversion and/or liner installation process. Different extrusion techniques may be applied to different fiber substrates and coating polymer in order to achieve maximum coating adhesion and liner stability.
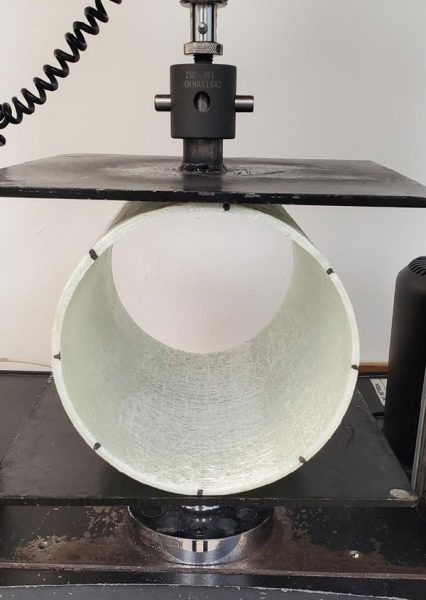
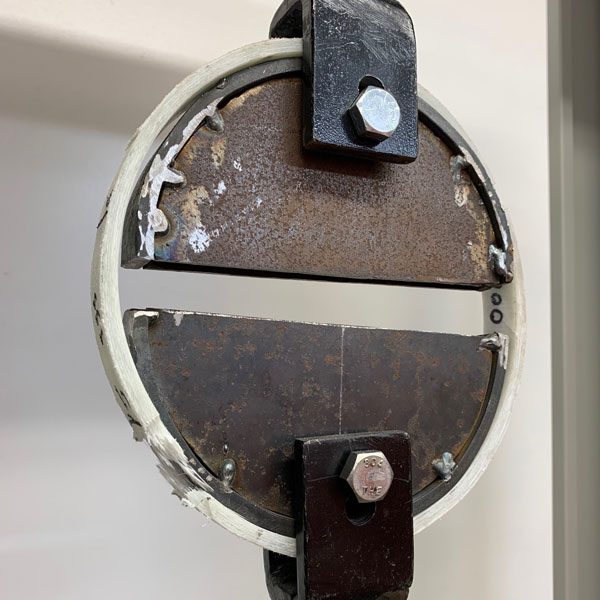
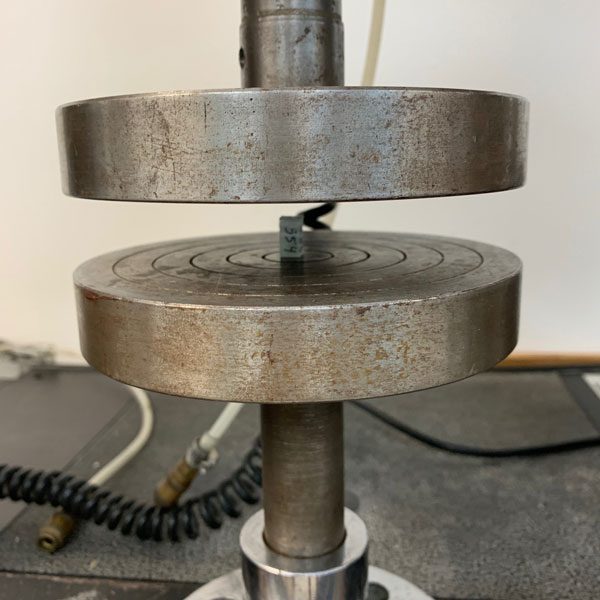
Image Courtesy of HTS Pipe Consultants, Inc.
The following table illustrates our in-process and final product inspection criteria which are carried out during/after manufacturing of coated liners (not limited to). Specimens/samples are taken across the web including the extreme edges on every roll of coated liner, unless specified. Destructive testing is also carried out to determine composite tensile strength and coating adhesion performance.
Inspection Criteria | Inspection Criteria and Critical Control Points Description |
Total composite thickness (coating on fiber material) | Measurements across the web using a weighted micrometer (constant pressure) with a dial graduated to 0.001 inches (ASTM D5119). Microscopic evaluation of cross-section of composite is randomly performed to determine coating integrity and saturation on fiber materials. Compression level during extrusion is also monitored to ensure total composite thickness meets required thickness and maximum coating adhesion. |
Total composite weight (coating on fiber material) | Measurements across the web (ASTM D751) Includes testing of plain felt rolls before extrusion coating. |
Finished width and length of liner | Measured and recorded for everyroll on Customer’s Inspection Report. |
Coating adhesion (heat weld) | Destructive heat weld method (ASTM D413). |
Coating adhesion (Styrene immersion +1hrs at room temp / 180F) | Destructive testing where specimens are immersed in styrene +1 hour. TPU/TPO coating must remain intact on fiber materials. |
Break strength and elongation (2in) | Destructive testing to determine tensile load or force required to rupture materials (ASTM D461) |
Dimensional stability | Measures the change in dimensions (machine and cross machine directions) on exposure to static heat 100oC (ASTM D1204). |
Hydrostatic resistance (Mullens) | Measures the resistance to water penetration under pressure and provides pressure readings up to 1500 PSI (ASTM D751A). Test also validates integrity of TPU/TPO coating on fiber materials (no pin holes and light coating spots). |
Coating gloss finish | Measures the consistency of gloss at 60o angle (ASTM D523). |
Coefficient of friction | Measures the slip properties when sliding to itself or over another substance (ASTM D1894). Testing by manufacturing lot / polymer type. |
E Squared also works closely with reputable resins suppliers in the USAto ensure E Squared TPU/TPO Flexpipe™ liners are compatible with thermosetting resin systems used in the industry. Application testing is performed to establish coating-resin compatibility and thermal resistance to withstand the initiation temperature and chemistry used in the curing of impregnated liners. It is also important that the initial CIPP structural requirements which includes flexural strength, flexural modulus and tensile modulus in reference to ASTM F1216 are met/exceeded for coated liners with impregnated resin system. Coating adhesion is tested using hot styrene at 180F and TPU/TPO coating must remain intact without defects, delamination and blistering.
In conclusion, the art of manufacturing high quality coated felt liners requires a detailedquality control and testing program, supported by high-precision die extrusion process. E Squared adopts a wholistic approach to quality control and assurance, which includes sustainable sourcing (USA-made materials and PFOA/PFAS free materials), evaluation of incoming raw materials, monitoring of critical control points in the extrusion process to assessing the final product performance. We also focus on staying up-to-date with industry needs and technology advancements for continuous growth and innovation and ability to better support our customers and industry partners.
References
ASTM F1216-22 Standard Practice for Rehabilitation of Existing Pipelines and Conduits by the Inversion and Curing of a Resin-Impregnated Tube
ASTM F1743-22 Standard Practice for Rehabilitation of Existing Pipelines and Conduits by Pulled-in-Place Installation of Cured-in-Place Thermosetting Resin Pipe (CIPP)
ASTM D5813-04 Standard Specification for Cured-In-Place Thermosetting Resin Sewer Piping Systems
NASSCO CURED-IN-PLACE PIPE (CIPP) INSTALLATION, PERFORMANCE SPECIFICATION GUIDELINE (PSG), March 2021